Company News
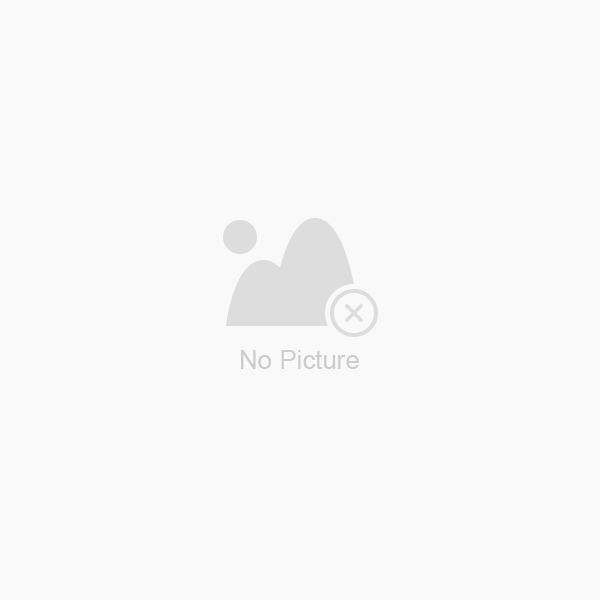
The correct choice of injection molding machine model and specification before use has a great impact on the production cost, quality and efficiency of injection molded products.
How to choose the right injection molding machine?
1. Choose the right series according to the plastic and finished product
As you know, there are many series or types of injection molding machines. So at the beginning, we need to determine which series or which type of plastic machine is suitable for you. For example, the material or product has different properties such as thermosetting or thermoplastic, single color, two-color or multi-color, sandwich or mixed color. Some products require higher production conditions, such as closed-loop, high precision, ultra-high injection speed, high injection pressure and fast production speed. By analyzing the plastic and finished products, we can decide the series of injection molding machine.
2. Choose a large enough machine clamping force according to your mold
We can determine the required drawbar distance, mold thickness, minimum mold size, platen size, etc. according to the mold size.
The height and width of the mold should be smaller or at least less than one side of the tie bar distance.
It would be better if the height and width of the mold are between the platen size.
The thickness and height of the mold are within the mold thickness of the injection molding machine.
The thickness and height of the mold is larger than the minimum mold size. A mold that is too small is also not suitable.
3. Enough strokes to remove the product
According to the mold and product size, we will judge whether the opening stroke and ejecting stroke are enough to take out the product. The opening stroke should be at least twice the size of the product in the opening and closing directions. The opening stroke should be larger than the length of the vertical sprue.
The ejector stroke should have enough space to eject the product.
4. Sufficient clamping force
When the molten plastic material is injected into the mold cavity under high pressure, high pressure will be generated inside the mold. Therefore, if there is not enough locking force, the mold will open and the material will leak, even causing accidents to the mold and the operator. It is very critical to have sufficient locking force.
There are several ways to calculate the locking force.
- Based on the product dimensions, we can obtain the projected area in the open and closed mold directions.
-Mold internal high pressure = projected area (cm2) * number of cavities * cavity pressure (kg/cm2)
The mold cavity pressure varies depending on the material. Usually we can take 350-400kg/cm2.
The injection process can only be successful if the clamping force is greater than the internal pressure of the mold trying to open the mold. For safety reasons, the clamping force should be greater than 1.17 times the in-mold pressure.
At this point, we can roughly determine the specifications of the clamping unit and the clamping tonnage. In the next procedure, we will decide which screw in the injection unit is suitable.
5. Full shot or full shot
Depending on the weight of the finished product and the number of cavities, we can check the right injection weight and the right screw diameter.
For better stability, the injection weight of the machine should be at least 1.35 times the weight of the product. In other words, the product weight should be 75% lower than the injection weight of the molding machine
6. Good shot
We can roughly understand the screw L/D ratio and injection pressure, etc. Some engineering plastics need high injection pressure and suitable screw L/D compression ratio. In order to get better finished products, we need to consider injection pressure and L/D ratio when choosing a screw.
In general, a smaller diameter screw can produce higher injection pressure.
7. Faster injection
Some plastic parts need higher injection speed to get a stable shape, such as thin-walled products. In this case, we need to check if the injection speed is sufficient and check if the machine needs to be equipped with accumulator, closed loop controller, etc. Generally speaking, under the same conditions, a screw with higher injection pressure has a lower injection speed, and conversely, the lower the screw injection pressure, the faster the injection speed. In short, when choosing a screw, we need to consider injection speed, injection volume, and injection pressure.
If you want to know more information, please contact us.
-
LSF308 making box machine
-
micro injection molding machine LSF68S
-
CE certified plastic fruit basket making machine
-
CE certified plastic paint bucket making machine
-
68ton small sized plastic injection molding machine
-
LSF258 full automatic plastic cup making machine
-
High Productivity Dispensing Machine for PVC Label Patch for Manufacturing Plastic Products Used Condition
-
High Productivity Dispensing Machine for PVC Label Patch for Manufacturing Plastic Products Used Condition
-
High Productivity Dispensing Machine for PVC Label Patch for Manufacturing Plastic Products Used Condition
-
High Productivity Dispensing Machine for PVC Label Patch for Manufacturing Plastic Products Used Condition
-
JY-160S2 Plastic Injection Molding Machine
-
DRUM MIXER
-
VIBRATING SCREEN MACHINE
-
POWERFUL CRUSHER
-
Injection Plastic Computer
-
Intelligent Injection Molding Computer
-
High quality vertical injection molding machine
-
Best price syringe production line medical disposable syringe making machine
-
Small PET Bottle Injection Molding Machine / Preform Making Machine
-
Low Price Small Plastic Preform Injection Molding Machine
-
High-Speed injection molding machine controller
-
Small plastic bottle injection molding machine 180ton
-
Plastic injection moulding / molding machine price
-
Small Preform Injection Blow Molding Machine Price
Popular Searches
- plastic machine
- hydraulic bottle
- instruction
- Injection Molding Machine
- Plastic Injection Molding Machine
- Cap Making Machinery
- cap molding machine
- Bottle Cap Making Machine
- Plastic Cap Making Machine
- Cap Injection Molding Machine
- oil injection
- horizontal injection moulding machine
- small injection moulding machine
- Injection Moulding Machine
- Cap Making Machine
- slide tie